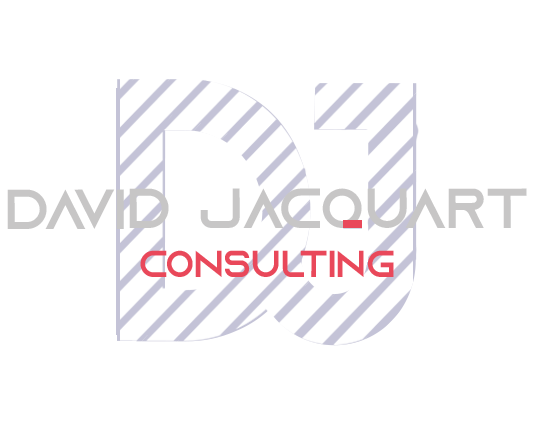
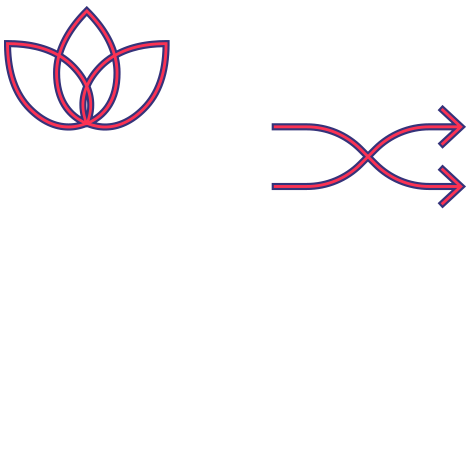
My vision
With very advanced skills in Production Systems Excellence and having been part of the first teams to spread good industrial practices in France, I understand in detail all the techniques and have actually implemented them all throughout my career.
Nevertheless, I support a holistic approach to industrial Excellence, the many techniques of which are tools serving our projects.
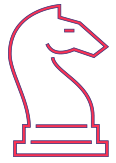
MY METHOD
I use this matrix to orient projects with customers.
It comes from merging knowledge acquired in my series of professional expertise, and putting it into practice as part of my operational functions.
Each of these bricks constitutes an analysis direction, determines my actions, and conceals the managerial tools and practices which I pick from according to the context.
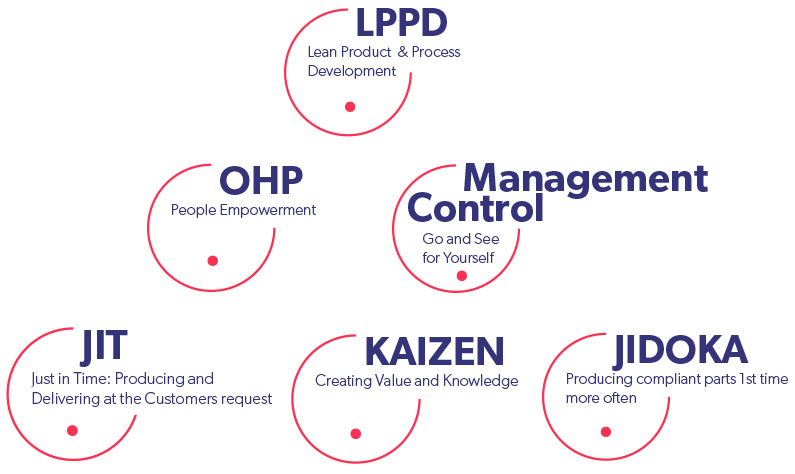
I support you to implement good industrial practices initiated by the TPS (Toyota Production System), where Kaizen and Respect for People take on their full meaning
CAREER & RESULTS
Thoroughly matured through seeking excellence, my career has been a series of extraordinary professional opportunities, which have been both a challenge and a pleasure to embrace.
See my career, judge my results!
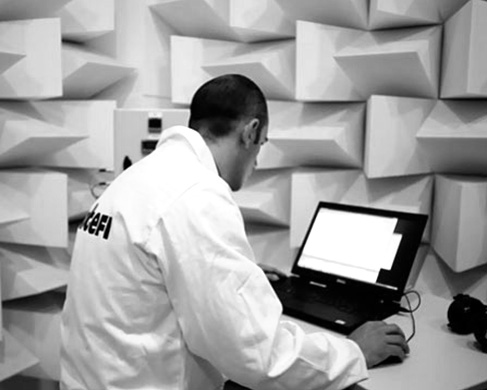
TESTIMONIALS
“Conventional consultants often tend to train on tools. With David, the real difference comes with action, in the field, where value is created. He knows how to alternate a level of expectation which helps question the status quo, with coaching and support for teams. He doesn’t have THE solution but leads your teams to find it!”.
_ > SOGEFI
Cédric Fournier // Operations Director North America


Development and deployment of the RSA MES with objective costs halved and OEE of the production lines rising strongly
TPM Internal Consultant: Significant OEE increase of the Engine and Gearbox manufacturing lines in industrialization phase (>92%), and operating costs halved (launch of the D engine – Twingo)

start-up of the D engine,
at Renault


+30% productivity a year at the Marckolsheim plant and then the "Acoustic and Soft Trim" division for FAI (13 plants in Europe).

at Faurecia



Michael Ballé’s coaching (ESG Consultant/ Shingo Prize) for 4 years, and immersion training with Toyota in Nagoya have allowed me to lastingly impact all the company's organisations, from Order taking to production .
Productivity gain of 15-20% a year, supporting the results through the economic crisis (2008) and helping finance R&D in a context of strong technological renewal.
Deployment of the SES (Sogefi Excellency System) in 10 plants worldwide (Europe, NAFTA, Asia)

from installation of the new
production system
at MARK IV


First LPPD workshops for a Tier 1 automotive equipment manufacturer : industrial investments are optimized and greatly reduced over very short periods of time (2 M$ in one week!)

for OREST, right
from first projects

Implementation of the Production Organization, creation of the Industrialization / Methods, Maintenance, Purchasing departments, Reorganization of the Quality department
Upgrading of the Product range, diversification of the Major Brands Customer portfolio: Operating Results x4 the first year, then + 30% per year
Automation of repetitive and "basic" tasks, allowing the professionalization of jewelers, and facilitating recruitments

by 6 in 4 years



Development and deployment of the RSA MES with objective costs halved and OEE of the production lines rising strongly
TPM Internal Consultant: Significant OEE increase of the Engine and Gearbox manufacturing lines in industrialization phase (>92%), and operating costs halved (launch of the D engine – Twingo)

start-up of the D engine,
at Renault


+30% productivity a year at the Marckolsheim plant and then the "Acoustic and Soft Trim" division for FAI (13 plants in Europe).

at Faurecia



Michael Ballé’s coaching (ESG Consultant/ Shingo Prize) for 4 years, and immersion training with Toyota in Nagoya have allowed me to lastingly impact all the company's organisations, from Order taking to production .
Productivity gain of 15-20% a year, supporting the results through the economic crisis (2008) and helping finance R&D in a context of strong technological renewal.
Deployment of the SES (Sogefi Excellency System) in 10 plants worldwide (Europe, NAFTA, Asia)

from installation of the new
production system
at MARK IV


First LPPD workshops for a Tier 1 automotive equipment manufacturer : industrial investments are optimized and greatly reduced over very short periods of time (2 M$ in one week!)

profit for OREST, right
from first projects


Implementation of the Production Organization, creation of the Industrialization / Methods, Maintenance, Purchasing departments, Reorganization of the Quality department
Upgrading of the Product range, diversification of the Major Brands Customer portfolio: Operating Results x4 the first year, then + 30% per year
Automation of repetitive and "basic" tasks, allowing the professionalization of jewelers, and facilitating recruitments

These exceptional results can
be yours tomorrow!
There’s more:
Your customers will appreciate your production quality, they will be better served, at optimized costs, and will enjoy a constructive and solid relationship again.
Your collaborators will be (re)motivated and have all the means to perform their jobs better, their work conditions will be improved and the more motivated ones’ desire to learn is satisfied
Your products will generate value because you closely follow users regularly, by establishing growth creation progress loops.
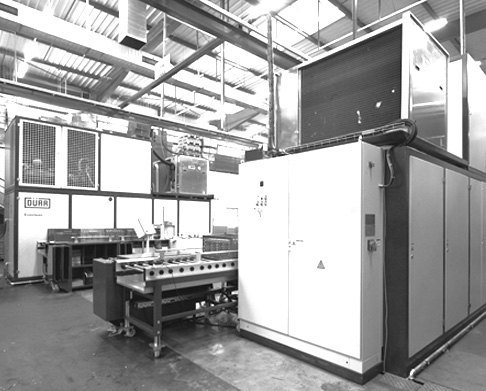
TESTIMONIALS
“ David is the best continuous improvement consultant I have seen in for the industry. He has a unique ability to take a group away with him. Remarkably enough, he guides his audience towards the acceptance of all the actions that will be implemented. His interventions are highly appreciated internally.
David has impressive knowledge and experience of the full range of tools and techniques in management and continuous improvement. I’ve always seen him achieve significant results, quickly. I have rarely seen this from other consultants, who are generally more dogmatic… ”.
_ > ALPENTECH
Sébastien Vallée // Managing Director
EXPERTISE
My Value proposal
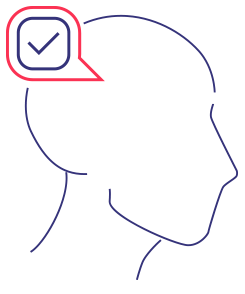
I do.
What I do with you
Reconciling or conciliating the conduct of operations with the strategic vision of the director or the owner
Installing, correcting or optimizing the operational conduct of an activity by developing an Action Plan, and its achievement
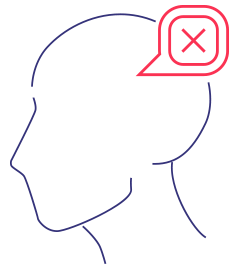
I do not.
What I don’t do
I do not train in Lean Management or in the peripheral techniques surrounding it. I use them to obtain operational results.
I do not submit a “report”. I analyse and I act.
I do not advise: I support, I create value and I transmit knowledge.
FOCUS
The Luxury sector in France has to meet a number of challenges to maintain its pace of growth
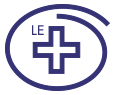
I work in Industry and Services, and I also had the opportunity to develop unique expertise for the Luxury sector
Luxury
Through my various support missions and as Industrial Director with a major manufacturer in the French jewellery industry, I used all my operational techniques and my experience to meet a number of these challenges.
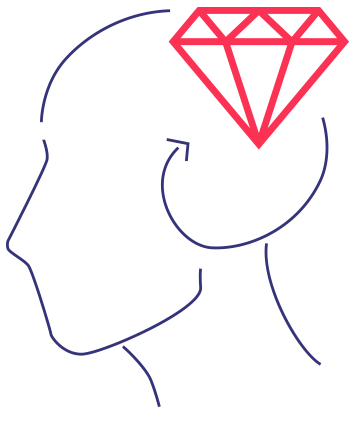
RECONCILING
Reconciling a strong Art business culture, while dynamizing the company, i.e. producing significant operational gains, while preserving the creative core and habits of the industry
IMPROVING
Improving the plants’ development capacities, to better respond to the designers’ demands
TRANSMITTING
Bringing technology and engineering science to serve the art business
RELEASING
Reconciling a strong Art business culture, while boosting the company, i.e. producing significant operational gains, while preserving the creative core and gestures of the industry
ACCELERATING
Accelerating the Time-to-market to follow the customer’s pace and maximize growth
CONSERVING
Conserving the technical and gestural know-how which are the basis of this industry
GROWING
Growing the production capacities to satisfy an always strengthening demand, without distorting production
OPTIMIZING
Optimizing the working capital, in a sector where the raw materials are expensive
INTEGRATING
Integrating an overall safety-security vision in the company’s operations, which handles precious raw materials, and manufactures finished products that are more so
CAPTURING
Capturing purchase intentions close to customers, especially by avoiding deceptive waiting times
Let’s get in touch with the Real Operational Excellence
for your company
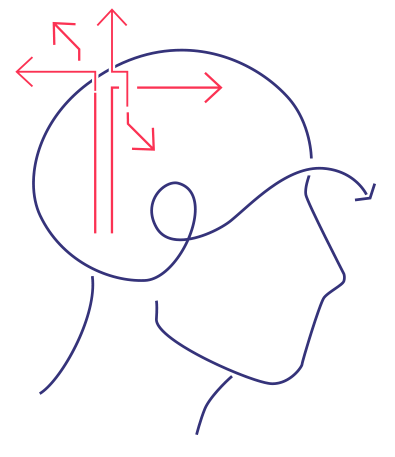
My Values
Through my personal pathway and in my professional career, I believe that I have forged key values, which inform my behaviour and which I share in my work.
Let’s share them?
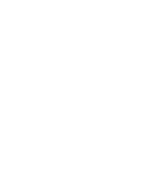
A DRIVER
CHANGE
Because change is always challenging us to become better, it is a driver for me.
Not only do I accept change but I become its agent, the trigger
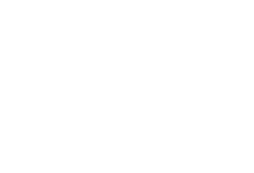
A PASSION
PEOPLE
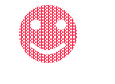
I have adopted this Toyota motto which appears on the walls of all the group’s plants: “Develop your collaborators to develop your Business”.
Because people are the top component of any production system, we are duty bound to take care of one another.
Taking the example of the TPS, improving the health and well-being at work of collaborators and managers is central to all my projects.
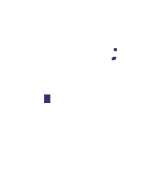
A NEED
TRANSMISSION
As long as I can remember, I’ve always wanted to learn. And then, over time, I have felt the need to experiment and put my knowledge into practice.
Throughout my professional life, I have alternated between Specialist and Operational jobs.
Now, my work only has meaning in the lasting transmission of what I’ve learnt and experienced, to my customers or my students*.
* At UNISTRA, for degrees and masters in Maintenance and Industrial Engineering. I am also an Apprenticeship manager (30 to 40 trained apprentices)
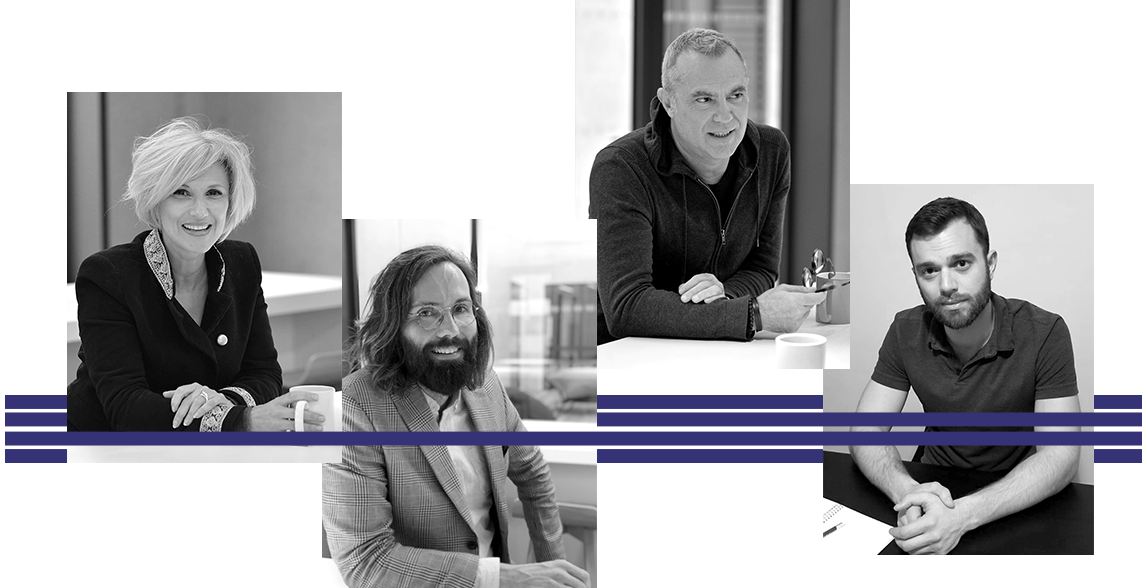
GIORDANI
JACQUART
CALLEGHER
BRITSCH
My team
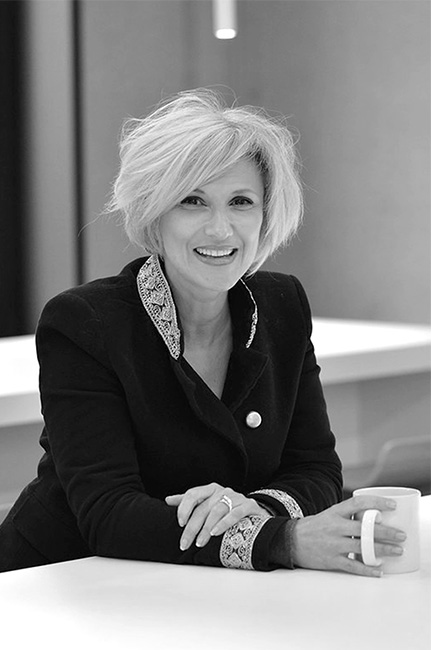
Senior Consultant
Some of my interventions come under the headings of "People Empowerment" and "Management Control" in the approach of David Jacquart Consulting, and especially:
- supporting directors and management teams with HR transfers and managerial postures linked to the organisational changes produced by the DJC interventions
- supporting the same teams with their postures and leadership to accompany the change itself
- coaching and personal development of the director

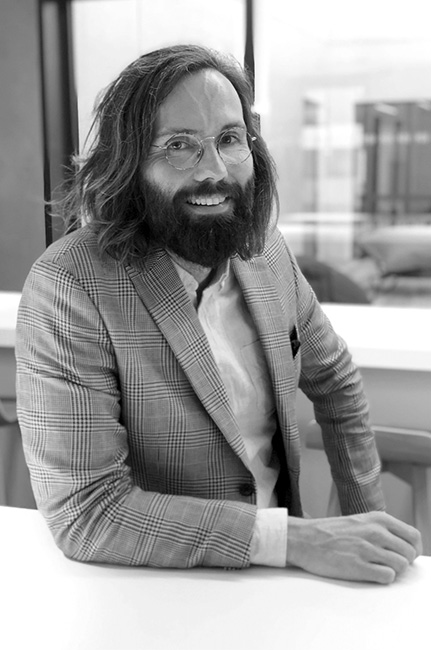
Junior Consultant

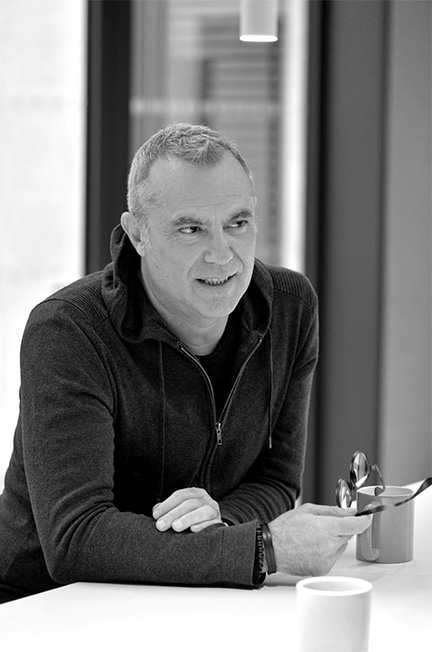
Senior Consultant
I created David Jacquart Consulting and built my team to create added value, greater knowledge and more well-being for directors and their employees.
We accompany directors in the more critical life phases of their company, we support them by optimising their actions and letting them save time.
We take care of staff teams, by concretely improving their work conditions and by preserving their mental loads.
Grounded people, Humanity fans!

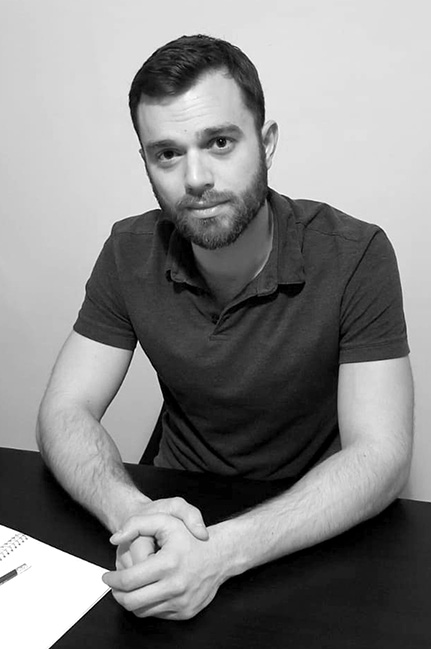
Junior Consultant & North America Business Development

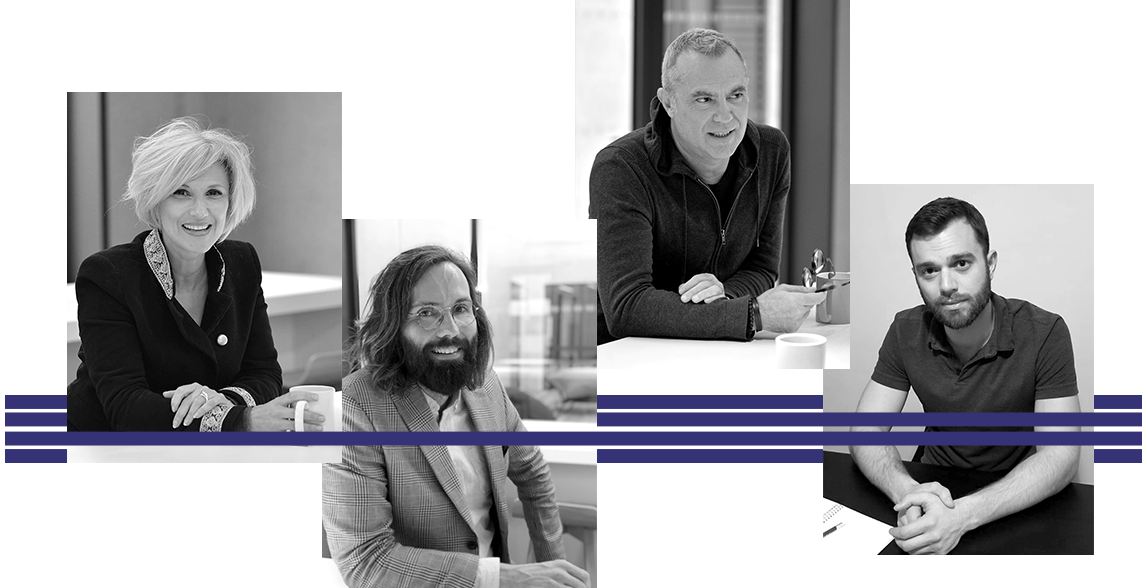
GIORDANI
JACQUART
CALLEGHER
BRITSCH
My team
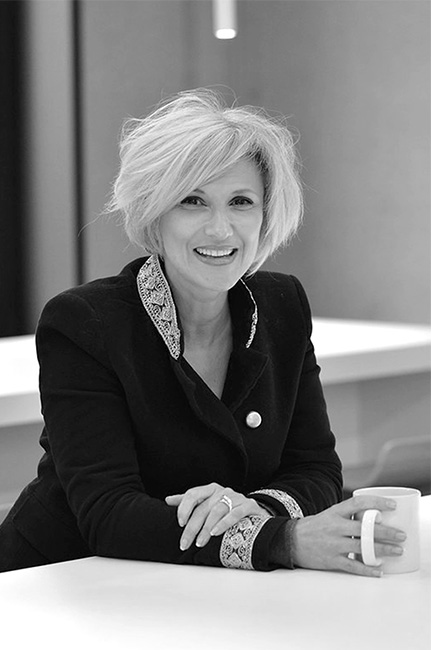
Senior Consultant
Some of my interventions come under the headings of "People Empowerment" and "Management Control" in the approach of David Jacquart Consulting, and especially:
- supporting directors and management teams with HR transfers and managerial postures linked to the organisational changes produced by the DJC interventions
- supporting the same teams with their postures and leadership to accompany the change itself
- coaching and personal development of the director

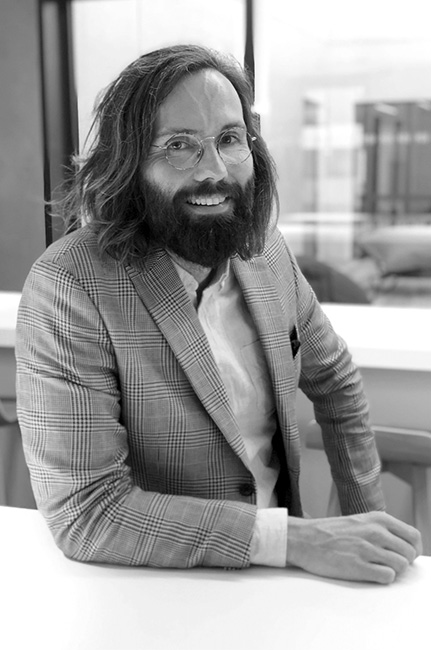

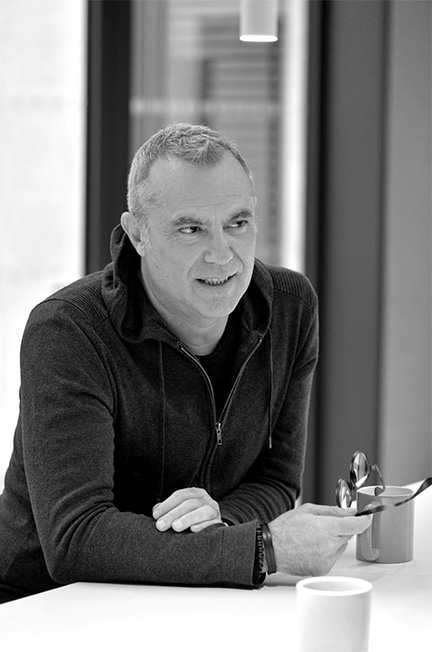
Senior Consultant
I created David Jacquart Consulting and built my team to create added value, greater knowledge and more well-being for directors and their employees.
We accompany directors in the more critical life phases of their company, we support them by optimising their actions and letting them save time.
We take care of staff teams, by concretely improving their work conditions and by preserving their mental loads.
Grounded people, Humanity fans!

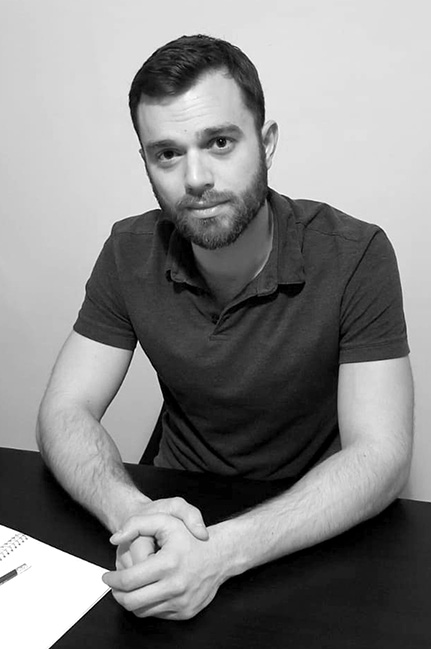
Junior Consultant & North America Business Development

My services
3 very personalized services for achieving results in the short, medium and/or long term
01 Quick Wins
[ Express R.O.I! ]
In a few days, I undertake corrective actions with you which directly affect the company’s economics and industrial operations. The results and ROI are immediate.
Examples :
> Identification of hidden dependencies
> Immediate improvement of the production processes
> Increased production rates
> Improved working conditions
02 Management Mob
[ MANAGEMENT MOBILIZATION ]
In the medium term, we work together to realign the financial and industrial strategies, and to share them with the management team.
A re-mobilized management team means the whole enterprise is going in the same direction!
03 INDUSTRIAL DYNAMIZATION
[ INDUSTRIAL DYNAMIZATION ]
In the long term we begin an in-depth transformation of your industrial tool.
By optimizing the installed Equipment, by providing it with additional activity and by transmitting knowledge to your operational teams, I dynamize the company’s industrial potential in a lasting way
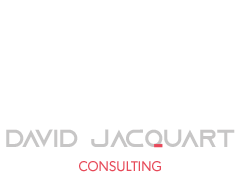
Digitization in the industry is particularly efficient, provided that its human and organisational preliminaries are in place.
For all my services, I support you to implement industrial digitization that is controlled and value creating.
Member of the Great East Professional Consulting Chamber
Member of the Alsace Businesses Buyers and Sellers Association
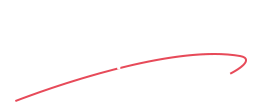
Contact us
David Jacquart Consulting is a company incorporated under French law, based in Strasbourg, France.